Via libera alla scala in cemento fabbricata digitalmente
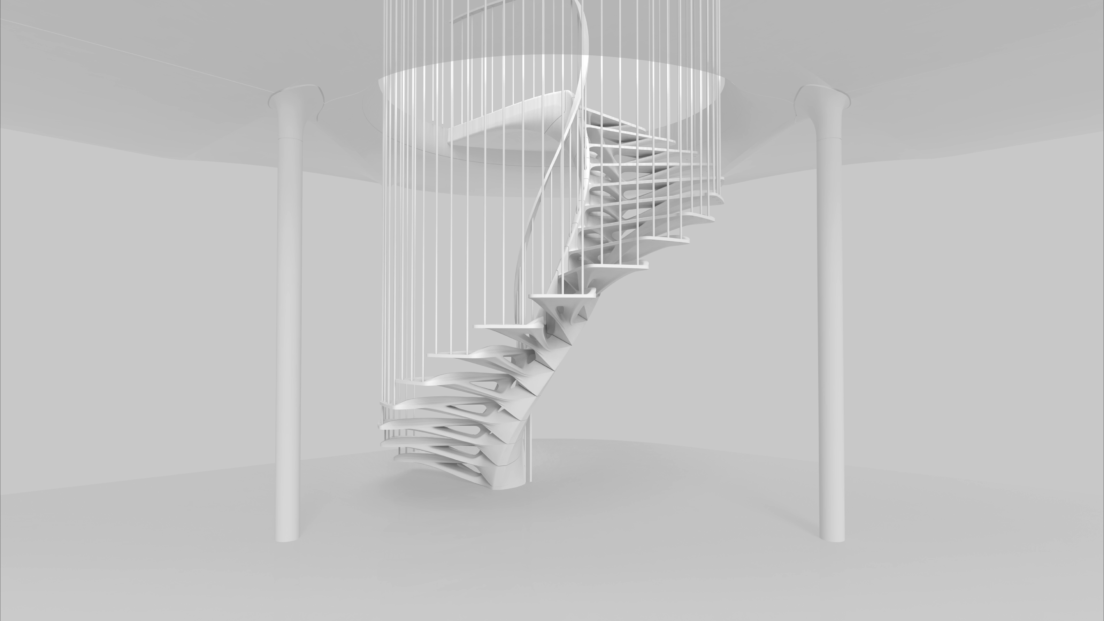
La prossima unità di NEST, l'edificio di ricerca e innovazione dell'Empa e dell'Eawag, si chiama "STEP2". Per circa due anni, i partner della ricerca e dell'industria hanno lavorato su diverse innovazioni nei settori dell'economia circolare, della fabbricazione digitale e industriale, dell'involucro edilizio e dei sistemi energetici, trasformandole in prodotti pronti per la costruzione. Una di queste ha ora raggiunto un importante traguardo: una scala unica al mondo, realizzata con casseforme stampate in 3D e precompressa con un'innovazione dello spin-off dell'Empa "re-fer", ha superato i test finali del prototipo.
È una delle grandi sfide della prossima unità NEST “STEP2”: una scala di cemento la cui forma ricorda la spina dorsale umana. Sebbene l’unità sia ancora in fase di progettazione, alcune parti della scala sono già state prodotte come prototipi. Perché l’unità persegue un grande obiettivo: verrà costruito solo ciò che ha un futuro nel settore edile. Insieme, i partner lavorano costantemente per essere pronti per il mercato – e questo è anche il caso della scala.
“Negli ultimi due anni, il team di progetto ha sviluppato insieme un concetto completamente nuovo per la produzione di componenti in calcestruzzo personalizzati. Questo è stato possibile solo perché gli esperti dell’intera catena del valore hanno lavorato insieme a livello visivo”, afferma con convinzione Enrico Marchesi, responsabile dell’innovazione del NEST e project manager di “STEP2”. Il team interdisciplinare del progetto è stato costituito insieme agli esperti di scouting e incubazione del partner principale BASF. È composto dallo studio di architettura ROK, responsabile della gestione del progetto, dalla Cattedra di Tecnologie Digitali per l’Edilizia dell’ETH, da esperti di stampa 3D della filiale BASF Forward AM e della società di stampa 3D New Digital Craft, da esperti del produttore di calcestruzzo prefabbricato SW Umwelttechnik, da ingegneri dello studio di ingegneria WaltGalmarini e da esperti dello spin-off Empa “re-fer”.
Soluzioni personalizzate
La scala “STEP2” dimostra in modo impressionante come le strutture in calcestruzzo possano essere realizzate con l’aiuto della progettazione assistita da computer e delle più recenti tecnologie di stampa 3D. Utilizzando casseforme stampate in 3D, è possibile creare forme più complesse rispetto alle precedenti casseforme speciali. Allo stesso tempo, la quantità di materiale richiesto può essere notevolmente ridotta.
Il processo consente di creare soluzioni di calcestruzzo personalizzate, che possono essere adattate in modo ottimale alla rispettiva applicazione e avere un elevato livello di dettaglio. Inoltre, ha anche un grande potenziale nel restauro, ad esempio nella ristrutturazione di edifici storici.
Alta complessità
Il progetto della scala proviene dalla Cattedra di Tecnologie Digitali per l’Edilizia dell’ETH. Sulla base di questo, il team del progetto ha sviluppato un sistema di casseforme complesse e basate su parametri per i singoli gradini, che vengono prodotti con la stampa 3D. “Per noi era importante utilizzare la fabbricazione digitale in modo da poter produrre elementi in calcestruzzo estremamente filigranati. Un criterio chiave per il sistema era la riutilizzabilità della cassaforma per la produzione di più gradini. Allo stesso tempo, abbiamo dovuto tenere conto dei requisiti della stampa 3D e del materiale, nonché delle condizioni di riempimento della cassaforma”, spiega Benjamin Dillenburger, responsabile del team “Tecnologie digitali per l’edilizia”. Per soddisfare tutti questi requisiti, lo scambio all’interno dell’intero team di progetto è stato di fondamentale importanza.
“Affinché la cassaforma stampata in 3D possa essere utilizzata per diverse fasi, abbiamo utilizzato un rivestimento adeguato. In termini di sostenibilità, abbiamo optato per un materiale che può essere nuovamente staccato dalla cassaforma. Solo così possiamo garantire che il materiale sia separato per tipo”, afferma Jörg Petri di “New Digital Craft”. Lui e il team “Virtual Engineering” di “BASF Forward AM” hanno apportato al progetto il loro know-how pluriennale nel campo della stampa 3D.
“Per BASF Forward AM, il progetto è una pietra miliare importante per dimostrare che i materiali utilizzati sono in grado di resistere alle elevate esigenze. Rientra nella nostra strategia di realizzare casseforme con la stampa 3D come alternativa alla costruzione di stampi tradizionali”, afferma Anke Johannes, Direttore Vendite Europa di BASF Forward AM. Per il materiale della cassaforma, il team ha scelto il filamento Ultrafuse® PET CF15, grazie alle sue eccellenti proprietà per le applicazioni di casseforme per calcestruzzo. Alla fine, il concetto di produzione e assemblaggio degli elementi della cassaforma era pronto.
Il test di resistenza
Ora è arrivato il momento di trasformare le scale in realtà. SW Umwelttechnik ha prodotto i gradini nella propria fabbrica con l’aiuto della cassaforma. Come materiale è stato utilizzato il calcestruzzo fibrorinforzato ad altissima resistenza. “Il nostro calcestruzzo permette di realizzare forme molto sottili e complesse, che non potrebbero essere realizzate con il normale calcestruzzo armato. È fantastico poterlo dimostrare in modo così impressionante con la scala dell’unità “STEP2″”, afferma soddisfatto Klaus Einfalt, CEO di SW Umwelttechnik.
L’ufficio tecnico di WaltGalmarini è responsabile del calcolo e della valutazione della statica. Per verificare se i valori calcolati corrispondono alla realtà, i gradini sono stati inviati all’Empa. Lì sono stati sottoposti a varie prove di carico da parte degli esperti dell’Empa, sotto la supervisione dell’ufficio tecnico. Il primo prototipo composto da tre fasi, che sono state tutte testate singolarmente, ha soddisfatto ampiamente le aspettative e allo stesso tempo ha fornito nuovi risultati per ottimizzare il sistema.
Nel prototipo successivo, è stata messa alla prova non solo la statica ma anche la costruzione del sistema di scale. Tre gradini sono stati infilati l’uno sull’altro e bloccati insieme utilizzando il “memory-steel”, una tecnica di precompressione innovativa sviluppata dallo spin-off dell’Empa “re-fer”. Nel processo, le barre del tipo “re-bar R18” sono state collocate in cavità predefinite e ancorate meccanicamente. La precompressione è stata effettuata mediante riscaldamento elettrico. Successivamente, sono stati eseguiti ulteriori test per analizzare la capacità di carico dei singoli gradini e del sistema nel suo complesso. Il risultato: gli ingegneri hanno ritenuto il sistema complessivo affidabile.
“Sono molto soddisfatto che la scala non abbia convinto solo sulla carta, ma ora anche nella pratica. Questo rappresenta per noi una pietra miliare estremamente importante del progetto”, afferma Michael Knauss di ROK. Con questa “prova di concetto”, la produzione della scala finale può ora avere luogo – un altro passo importante verso la realizzazione dell’unità NEST “STEP2”.