Sustainable CO2 storage in the concrete plant
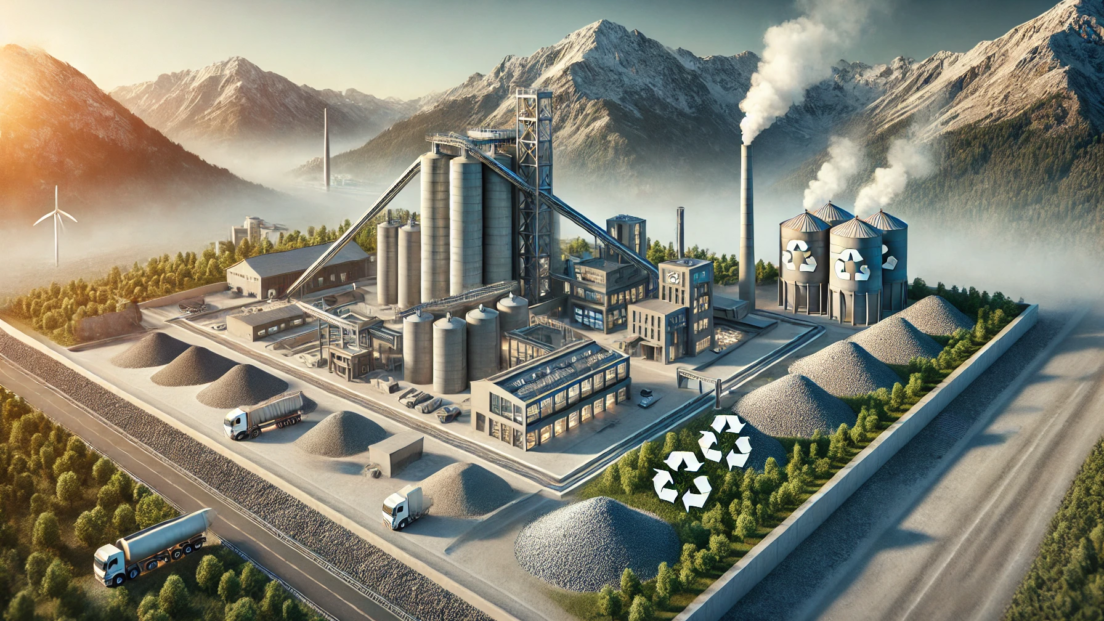
The Ch. Gerster AG gravel and concrete plant in Liechtenstein is the first company to use Neustark's CO2 storage process. This process helps to permanently bind CO2, thus reducing emissions in the construction industry.
The gravel and concrete plant of Ch. Gerster AG is the first company in Liechtenstein to offer the Neustark process for storing CO2. The CO2 is mineralised on site in Gerster’s concrete granulate called granulite, which in turn is obtained from demolition concrete. This granulate is also a component of Gerster’s Rainulit recycled concrete. “We are thus presenting a solution for reducing CO2 emissions in the construction industry,” says a statement from Gerster.
In the plant developed by the Bern-based ClimateTech company Neustark, gaseous CO2 of biological origin reacts with lime produced during cement production. This mineralisation process produces limestone again. As the CO2 would only be released again at a temperature of over 700 degrees, it remains permanently bound in the limestone and is therefore permanently removed from the air. According to Neustark’s own press release, the Ch. Gerster AG plant can permanently store 100 tonnes of CO2 per year.
Neustark now has 19 separation and storage plants, transforming the world’s largest waste stream – demolition concrete – and other mineral waste materials into carbon sinks. According to its own figures, the spin-off from the Swiss Federal Institute of Technology in Zurich(ETH) has so far permanently removed 1719 tonnes of CO2 from the air. Its goal is to reach 1 million tonnes by 2030.