K118: A building made from construction waste
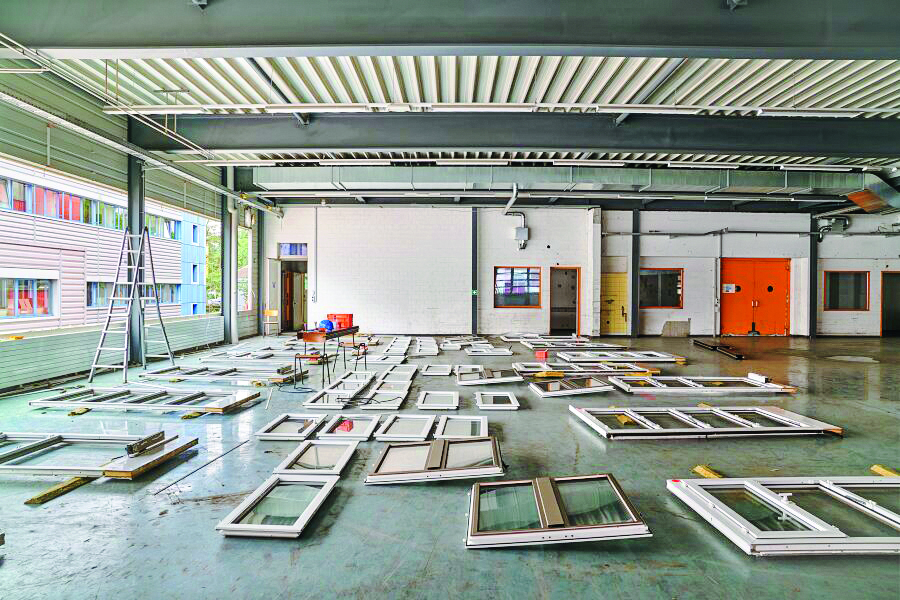
More recycling is not possible: The front building of building 118 on the storage area in Winterthur is being built exclusively from reused building materials.
A project that could hardly be more sustainable: the extension of hall 118 on the storage area in Winterthur ZH was increased by five floors. And wherever possible with reusable building materials. The presence of such materials from demolitions in the region was decisive for the current appearance. The building is not yet completely finished: “The construction should be completed in early 2021,” says Benjamin Poignon, architect and civil engineer at “baubüro in situ”.
The Abendrot Foundation, based in Basel, bought the Lagerplatz area from Sulzer Immobilien AG in 2010. The direction of focus was quickly clear to the pension fund, which is committed to sustainability: the already existing mixed use should be further developed in cooperation with the tenants. Several new studios of up to 60 square meters for start-ups and small businesses are planned for each of the upper floors.
Although the buildings and their footprints were to be retained, they were to be further developed in terms of energy and in accordance with legal standards. The “construction office in situ” is responsible for the project. The project managers Marc Angst and Pascal Hentschel sum up the concept: «Repairing what can still be used. Remove what disturbs or is no longer suitable – and add what is new. "
Finding building materials is half the time
The supporting framework consists of an used steel structure. Prefabricated facade elements made of wood, which are filled with straw insulation, are attached to this. Such simple ecological building materials as straw, excavated earth and wood accumulate in large quantities and can be processed and used with a minimal use of gray energy. They also ensure a pleasant room climate.
The slightly overhanging south facade in bright brick red-orange comes from the sheet metal facade of the former Ziegler print shop in Winterthur Grüze. The windows in the new recycling building are inconsistent, but overall they are consistent. In order for the insulation to meet today's standards, the glazing was doubled in nine windows, the others had sufficient insulation. The staircase on the east facade is over 30 years old and previously adorned the facade of the Orion office building in Zurich-West. 80 windows and facade panels made of granite, which are recycled for the balcony floors, also come from this building, which was erected in 1989. The respective components are not reprocessed – this differentiates the project from so-called downcycling, in which building materials are initially reworked in a energy-intensive manner.
The architects have already learned a lot from this unique pilot project: “It is the first time that we have reused a supporting structure. But we also noticed that there are components that are cheaper to buy than to reuse. For example, we have tried to reuse limestone sandstone. But the cleaning and preparation work was so high that we decided to buy a new one here, ”explains architect Poignon. The project also created a new job: component hunter. The “baubüro In situ” hired interns specifically for this purpose, who looked for suitable demolition objects and any reusable materials that might arise. But the architects, too, are always on the move with open eyes. Usable materials are dismantled and picked up by the architectural office with roots in Basel. The architects spend half of the time evaluating and procuring possible components. "In situ" did not have any problems finding the right material: of the approximately 7.5 million tons of construction waste that is generated in Switzerland every year, only 0.1 percent is directly reused, according to the Federal Office for the Environment (FOEN) has. «In situ» assumes that ten times more can be reused.
Book publication planned
If you think about the costs at this point: 4.8 million Swiss francs have been budgeted for the project so far. One of the stated goals was to build in such a way that it does not cost more than a completely new building. “It is difficult to make direct comparisons,” says Benjamin Poignon.
In general, “in situ” always relies on the reuse of materials during construction – even if rarely on this large scale. With its uniqueness, K118 has definitely attracted interested parties: A research and teaching project at the ZHAW University of Applied Sciences in Winterthur and a case study in environmental systems science at ETH Zurich accompanied the planning. Among other things, the environmentally relevant (waste, resources, lifespan, etc.) and legal as well as those relating to the construction process are examined. A joint publication is planned in cooperation with the Federal Office for the Environment: The book is intended to comprehensively shed light on the reuse of components in building construction and to make the knowledge and experience gained publicly available. ■
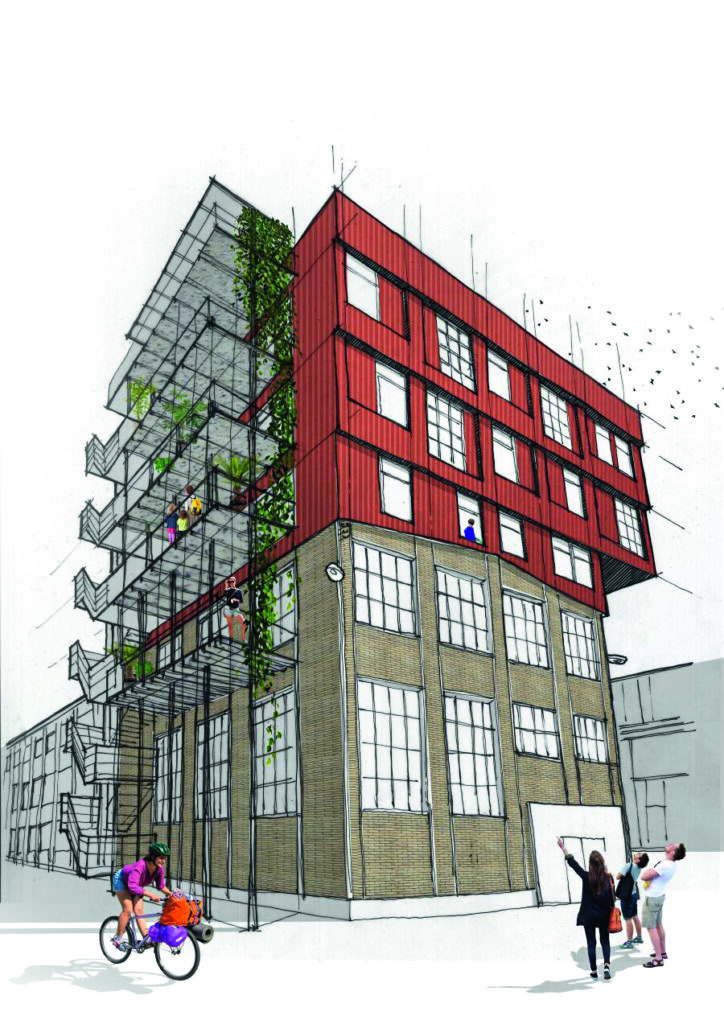