First use of CPC concrete slabs in building construction
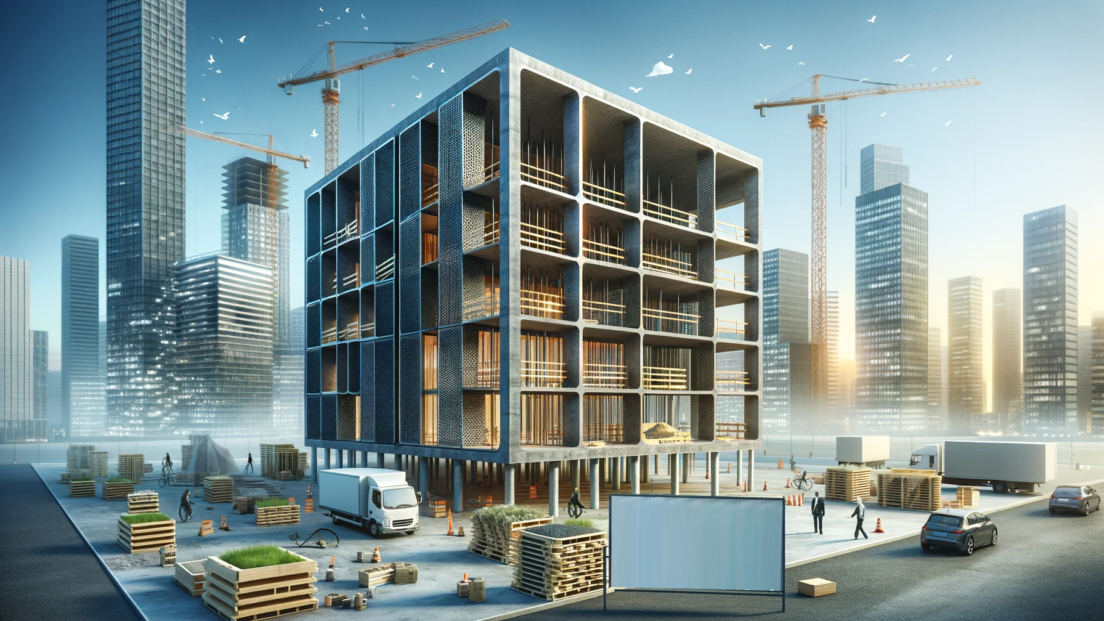
The Zurich University of Applied Sciences (ZHAW) is using CPC concrete panels in high-rise construction for the first time. These innovative carbon-reinforced concrete panels significantly reduce the carbon footprint and are recyclable. An innovation lab in Winterthur serves as the first application example.
The Zurich University of Applied Sciences(ZHAW) is using the CPC concrete slabs (Carbon Prestressed Concrete) it has developed for the first time in building construction. This refers to concrete slabs that are reinforced with prestressed carbon. According to a press release, an innovation laboratory has been created in Winterthur from these innovative components, which functions as an information and event centre for sustainable construction. The carbon concrete panels are not only recyclable, they also have a significantly lower impact on the environment than conventional reinforced concrete during production. “Thanks to the new lightweight construction method in concrete, we reduce the CO2 footprint by a factor of two to four and save up to 75 per cent material compared to conventional construction methods,” Josef Kurath, co-founder of CPC AG, a spin-off of the ZHAW, and developer of the carbon concrete panels, is quoted as saying in the press release.
The carbon concrete panels used for this purpose are currently being manufactured, processed, cut to the millimetre and assembled into building elements at Holcim ‘s first CPC plant in Germany. This preliminary work saves time during assembly on site, as there is no need for time-consuming on-site reinforcement work. “This results in much shorter construction times, which is a particular advantage for urban construction sites,” continues Kurath. Extensions or changes to buildings are also possible at any time. “Our carbon concrete construction system works in a similar way to Lego, but like a modern version of it, with customised components.” And CPC even has advantages over conventional building materials in the event of dismantling: 90 per cent of the processed material can be reused.